Thermo Chemical Reduction Method (TCR)
Shape and size stabilization technology of wood by Thermo Chemical Reduction Method (TCR) by which combustion gas of wood biomass is applied.
Modifed: 18 September, 2015
Created: 16 August, 2015
General problem of wood drying technology including smoke heat treatment
Smoke heat treatment will be defined as a direct heat wood drying method. This method dry the wood with the heat of combustion gas when the wood waste is burnt. However, a scientific verification to this dry technology had been hardly performed.
Up to now, scientific proof to this technology had been hardly performed. In addition, there are a lot of problems of this technology in the processing system, too. Therefore, social acknowledgment to this technology is not yet advanced.
On the other hand, the purpose of an ordinal wood dry technology (kiln dry method) is only to reduce moisture in wood. This technology is based on the experience rule that the dimensional stabilization of wood is steady by the moisture removal in wood by natural seasoning. This technology is also not scientific and repeats the trial and error by the means like allopathy.
High temperature drying method which is the main current of recent wood dryness is typical one. This method is mainly used for structural materials like beam and pillar which is difficult to dry.
However, a lot of radiated cracks occur internally in this method though the surface crack does not occur because of drying set.
Exactly, this technology is a cheating one, and the wound of this technology will be asked in the near future.
Problem of national policy, wood academy and wood industry.
- Japan converted the national policy to the establishment of a state on the basis of industries.
- Round-down of forestry.
- Depression of domestic timber by import liberalization of the imported timber.
- One of causes to which forestry and timber industry in Japan decline is rapid development of the wood industry. As a result, wood has become a mere industrial raw material. In conjunction with this, price reduction of timber is enhanced.
- Disciplinary of wood science has been made light of the research by which the material characteristic of wood itself is researched from a comprehensive standpoint.
- The industry related to the wood material like lumber mill was not able also to do new engineering developments.
- On the way to advance of the standardization of wood alternative, rough lumber producer was not able to commercialize an excellent function for wood itself originally.
- The neglect to be entirely-focused on the allopathy of ministries concerned promoted today’s decline further more.
Contributing factor to deformation and destruction of wood.
The tree should support the one’s own weight of tens of tons for a large tree, and resist the external pressure such as the winds and the snows.
Therefore, various prestress, that is, the field of internal stress, is produced in the trunk.
These internal stresses are caused by mutual interaction among such as growth stress, reaction wood, spiral grain , the moisture distribution, and gnarls.
These internal stresses become various trouble to us wood.
It is the internal stress to cause the deformation and the crack of wood.
(1) Internal stress caused in trunk —growth stress
Force formed in vertical direction of trunk

- From the outer bark side to 1/3 of radius in the vertical direction, tensile stress has acted. This stress becomes the maximum on the outer bark side, and becomes to 0 1/3 in the radius.
- From 1/3 in the radius to the center part, that is pith, the stress in the vertical direction changes into compressive stress. This stress becomes infinitely large in the part of pith.
(2) Internal stress caused in trunk —growth stress
Force formed in tangential direction of trunk
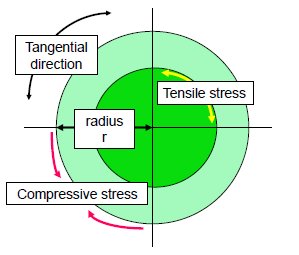
- Compressive stress acts on the peripheral side in the tangential direction of the trunk, and also tensile stress acts internally.
- The trunk balanced by these two stresses.
- When these stresses are free by lumbering, the cup is caused on the outside surface in the flat grain lumber.
(3) Internal stress caused in trunk —spiral and interlocked grain
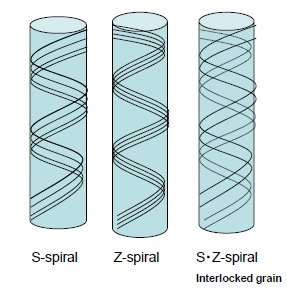
- The tree which grows straight forms the cell tissue like the spiral in order to support the trunk. When such a tree is sawed up, the lumbering goods are twisted and the ruggedness is caused on the surface of the lumber for interlocked grain.
- Such constitution is called spiral grain, and there are three forms shown in figure.
(4) Formation of reaction wood (For the sloping ground)
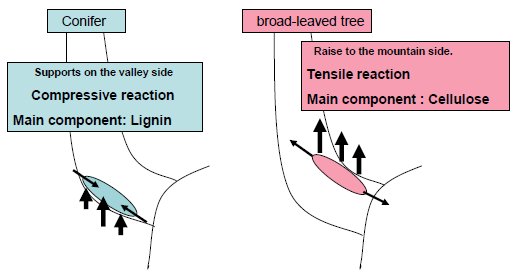
(5) Formation of reaction wood in the part of trunk.
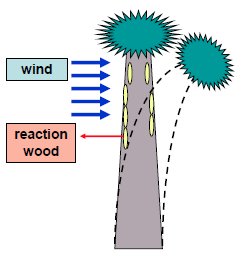
- In the environment which blows windy, reaction wood formed in the part of trunk.
- The tree that there is crown in the end part of stem like Agathis spp. and Parana pine, etc. is influenced easily by the wind, and a lot of reaction wood is formed in the straight part of trunk.
- As for such a lumber, warp and shrinkage in the longitudinal direction is large. However, if the size is steady, this lumber is suitable for a structural lumber because strength is high.
(6) Moisture distribution in the stem.
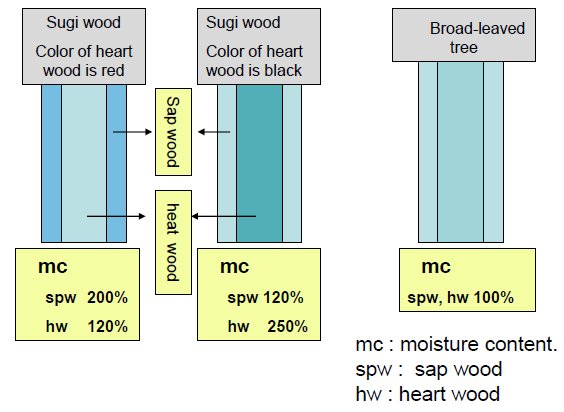
How is the stabilization of shape and the size of the wood material itself achieved?
- The deformation of wood, that is crack, bow, twist, collapse, etc. are a big troubles in the use of wood.
- The main one which became the contributing factor of these deformation was drought together in five items.
- Up to now, there was no technology which was able to remove or to relax these five contributing factors of deformation all at once.
- Having been done up to now is a method of removing moisture in wood which is the fifth contributing factor in all countries.
- That is, it is natural seasoning and kiln drying which chiefly uses steam.
- However, it is almost impossible to remove the contributing factor of four remainder only by this method. To solve this problem, the effort to upgrade the technology of bonding and the wood machine processing was continued.
- As a result, the wood resources has dried up rapidly by an industrial raw materialization about wood.
- It is a natural conclusion that related industry declines if the raw material is lost. The wood material industry is not reproduced except that the wood material itself commercialized.
Paradigm change concerning utilization of wood material itself.
- Wiping out of emotional belief to wood material. → Scientific proof to emotional function of wood.
- Review of belief to natural seasoning. → Breakaway from irrational means.
- Review of belief to artificial drying. → The uselessness of the machine system is verified.
- Related disciplinary of the wood material research is restructured from a comprehensive standpoint.
- Scientific specific and the commercialization of each tree species and their material function which has been used up to now based on experience rule.
- Essential standardization of each wood species.
- Digitalization of wood material function.
Smoke heat treatment technology
- General recognition of a related industry to the smoke heat treatment technology is low and an unscientific technology.
- However, this technology is the latest general science and technology by which shape and the size of wood are stabilized.
- This technology is one of the shortest technologies to achieve the society of making to low carbon.
- This technology is not only the best technology for effective use for wood material itself, but also becomes a core technology to manufacturing the engineering wood.
Smoke heat treatment → Thermo chemical reduction processing
- Smoke heat treatment is a technology which has used by wood turner experiencing since old times. Before the potter’s wheel was processed, the rough cutting wood treat by smoke in order to stabilize and dry.
- It is Mr. Ujiie to have used this technology to process the log for the first time.
- It is said that a distortion little becomes a hint as for the tree which burns by lightning when it is sawed up.
- This technology would understand the size of wood was stabilize in a short term and be highlighted.
- However, a lot of problems occurred because this technology was a halfway technology of the idea.
- I clarified that this technology was based on the thermo chemical reduction reaction for the first time, and also clarified the characteristic of the combustion gas which was basic of smoke heat treatment, and elucidated the mechanism of this processing method overall.
- And, I defined the expression “Smoke” of fuzzy by a clear science and technology term “Thermo chemical reduction”.
- This technology is named “Thermo-chemical reduction method” and “TCR” for short title.
Comparison between kiln drying (KD) and thermo chemical reduction processing (TCR)
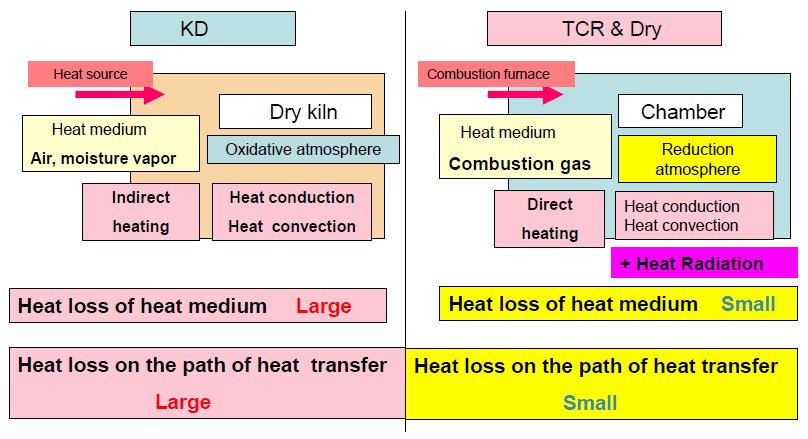
Difference of chemical reaction by oxidative and reductive atmosphere
Oxidative atmosphere
Oxidative deterioration of wood tissue by synergy effect of oxygen and heat.
Reduction atmosphere
Fixation and stabilization of organization with the self-organization between combustion gas element and chemical composition of wood tissue element in state of no oxygen.
Oxidation deterioration in wood under oxidation atmosphere
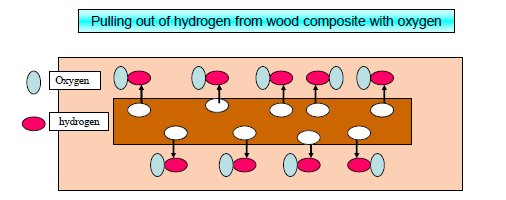
The heating air is used to dry wood at KD. In this case, hydrogen is pulled out from the composite of wood with oxygen included in air, and wood tissue does the oxidation deterioration.
The heating air accelerates the oxidative deterioration of wood as much more high temperature.
Actual example of oxidative deterioration of wood under oxidative atmosphere.
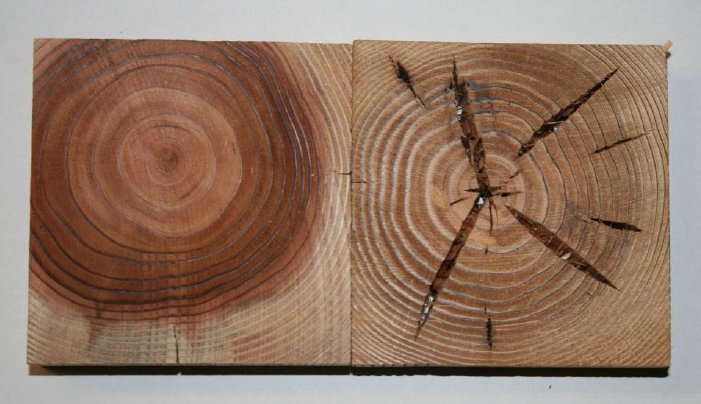
Left picture: TCR
Right picture: High temperature KD
- Only the surface of wood is rapidly dried at KD of the high temperature processing, and drying set occur on the surface of wood. Therefor, the crack does not appear on the surface of wood.
- However, a lot of cracks occur radially on the butt end.
- This crack accelerates so that the active oxygen may pull out hydrogen from wood chemical composition.
Self-organization of wood in reductive atmosphere
Pattern diagrams 1: Self-organization by various chemical reactions
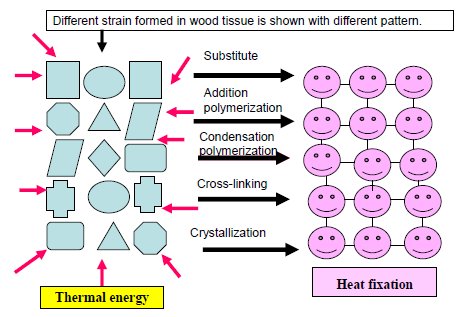
Pattern diagrams 2: Liberating and uniformly of strain formed in wood cell wall by thermal softening of lignin
Compression and tension strain formed with cellulose fiber in the cell wall were shown with spring model.
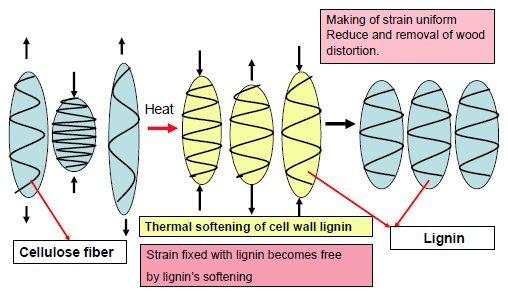
pattern diagrams 3
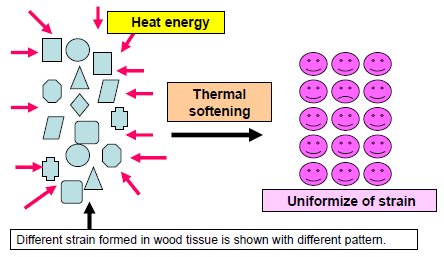
Concrete example of evidence which wood tissue self organized in reduction atmosphere
(1) Making of cell wall fixation
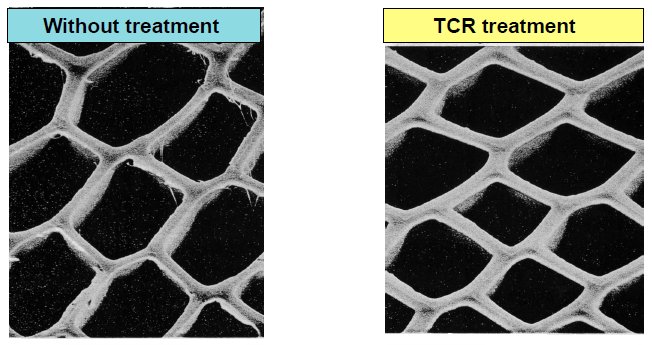
SEM photograph of butt end face of Italian poplar.
Cross sectional surface of TCR treatment is smooth and no scuffing.
- There is no flash and scuffing on the cross sectional surface of the TCR processing lumber.
- But, there are a lot of flash and scuffing on the cross sectional surface of natural seasoning wood.
- One of concrete examples which show that cell organization was fixed by self-organization.
(2) Fixation of stem organization to oil palm.
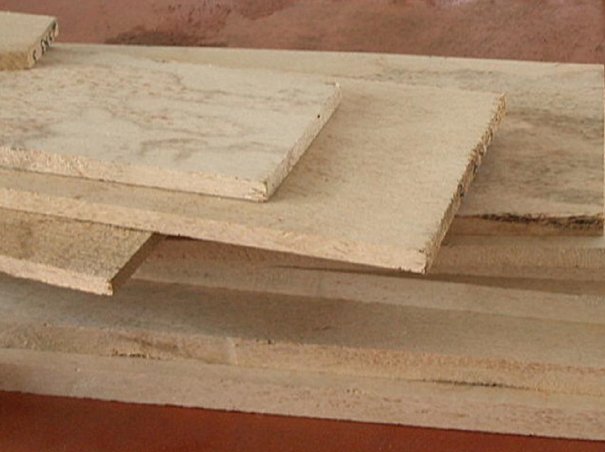
- The old-growth stem much more 25 years is cut down, because the harvest of fruits drops.
- The stem cut down is difficult reuse and abandoned because of high moisture content from 250 % to 500 %.
- The amount of this stem waste reaches about 0.2 billion tons par year in Malaysia and Indonesia.
- The self-organization of oil palm lumber by TCR was proven under the reductive atmosphere.
(3) Air-dry moisture content —Air-dry density
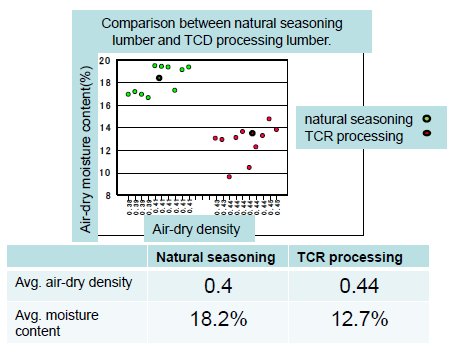
- The air-dry moisture content of the natural seasoning of Sugi lumber is average 18.2 %, and TCR processing lumber is average 12.7 %.
- The air-dry moisture content of TCR processing lumber decreases to natural seasoning lumber by 30 %.
- It shows that the part having an affinity to water exchange to hydrophobic by self-organization. As a result, The TCR lumber is stabilized to a surrounding humidity environment.
- That is, the swelling and the shrinkage according to the humidity change is decreased, and the distortion of the lumber is reduced.
(4) Shrinkage percentage to tangential direction
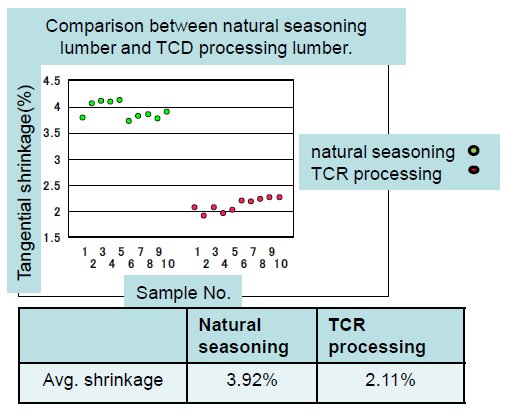
- Tangential shrinkage of natural seasoning lumber is 3.92 % on the average.
- Tangential shrinkage of TCR processing lumber is 2.11 % on the average.
- TCR lumber’s shrinkage is decreased about 46 % against natural seasoning.
- This result shows that new chemical bond by self-organization was caused between the composite molecules of the wood tissue.
- This result also becomes the evidence of the dimensional stabilization by TCR processing.
(5) Shrinkage percentage to radial direction
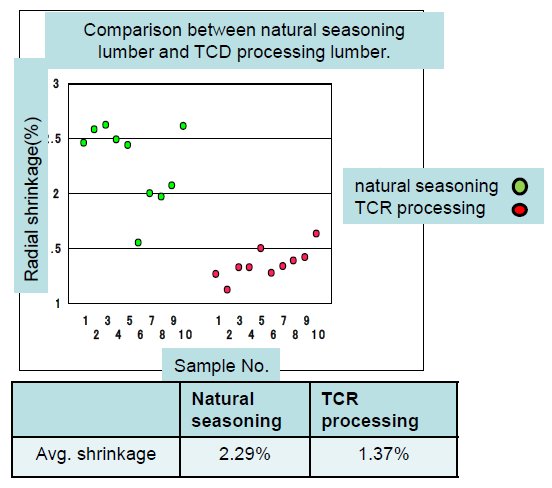
- Radial shrinkage of the natural seasoning lumber is 2.29 % on the average, and TCR lumber is 1.37 % on the average.
- The shrinkage percentage of the TCR lumber is decreased about 40 % against the natural seasoning lumber.
- This result shows that a new chemical bond by self-organization was caused between the composite molecules of the wood tissue.
- The ratio to the shrinkage percentage for each direction is 10:5:1 usually. This ratio becomes 10 and 6.5 respectively by the TCR processing for tangential and radial direction, and the shrinkage anisotropy is improved.
Mechanism of TCR
Heat and thermo-chemical environment in processing chamber.

(1) Heat and thermochemical environment in wood
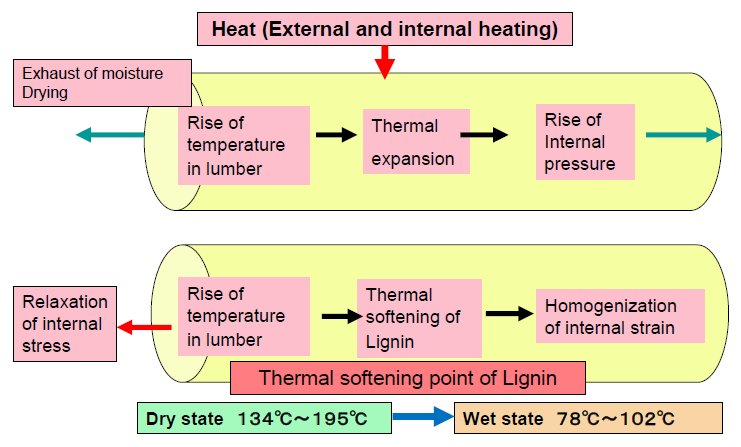
Difference of how to transmit heat in lumber between KD and TCR
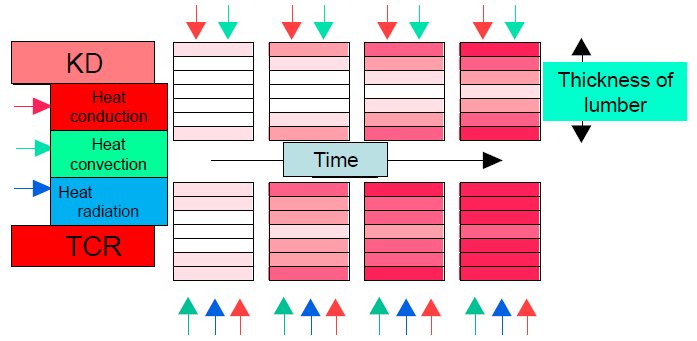
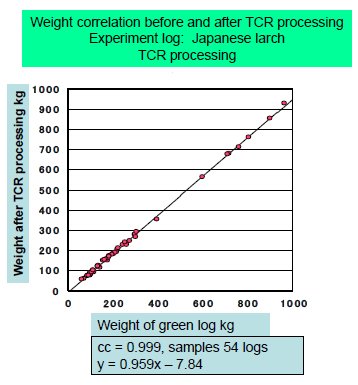
- Figure shows that the weight decrease rate after TCR is processed is constant regardless of the diameter to constant length of log.
- The log is uniformly heated by the effect of internal heating by heat radiation.
(2) Heat and thermochemical environment in wood (Heat vibration)
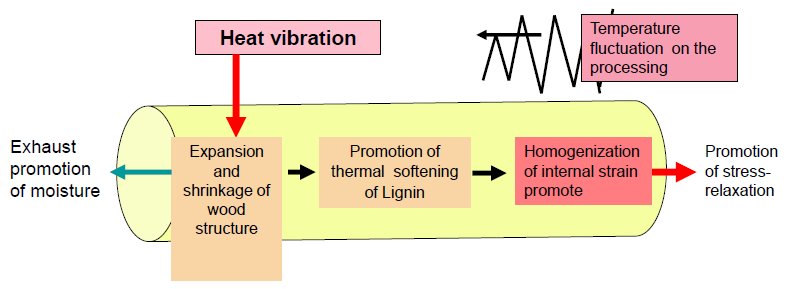
- Temperature fluctuation on the processing exchange into a kind of physical vibration, that is the repetition of expansion and shrinkage, in wood structure.
- The softened state Lignin in non-equilibrium state of moisture comes to move easily further by this physical vibration and homogenization of internal strain much more promote.
(3) Heat and thermochemical environment in processing wood (Superheated steam)
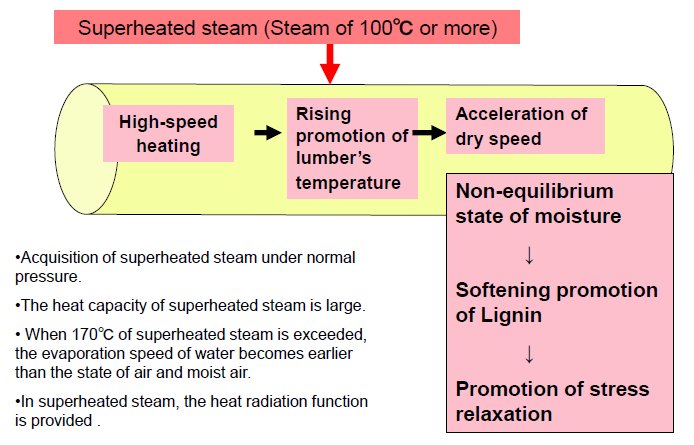
Comparison of evaporation speed inclinations of water by difference of heat medium
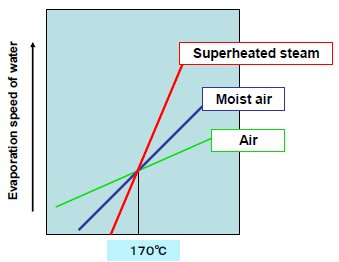
Thermal energy comparison of heat air and superheated steam
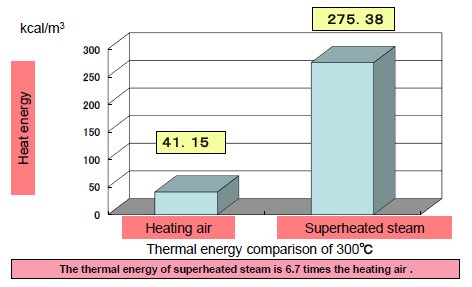
Effective utilization of superheated steam
- The moisture content of the processing lumber can be efficiently lowered by using the heat conduction characteristic of superheated steam with TCR.
- The green log of a high moisture content is processed effectively even if the processing temperature is raised up to 200 °C and much more, if it is in appropriate processing time.
(4) Black body radiation
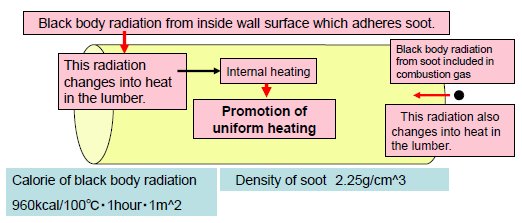
Black body radiation effect by soot, that is “unburned carbon”
- When the size of soot of one lump is assumed to be a globe of 0.1mm in the diameter, and the soot of 20 kg is generated by the combustion gas, the surface area of the total soot becomes 533.68 m2.
- The radiant heat obtained from the unit surface area of soot when the temperature in the furnace is 100 °C becomes 960 kcal.
- The calorie obtained from the surface of the soot of 533.68 square meters becomes about 512000 kcal. So, the radiant heat will reach 12,300,000 kcal in 100 °C and 24 hours.
- When the moisture content of the wood used for the fuel is 50 %, the calorific value of the wood waste material is 2500 kcal/kg.
- Therefore, 12,300,000 kcal corresponds to 4.92 tons of the wood waste.
- This heat radiation energy is absorbed directly to wood, and can raise the temperature of the lumber from the inside efficiently by changing into heat.
(5) Thermochemical reaction under reductive atmosphere
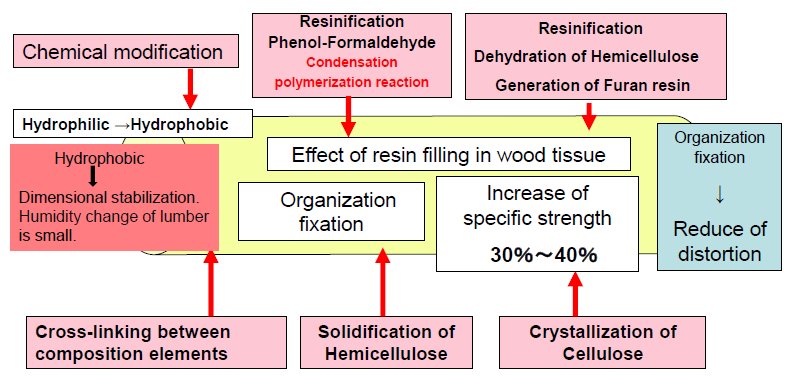
Theoretical background of Nomura type TCR technology
- The organization of wood is thought to be a state of a kind of solid solution by usually containing water from 50 to 80 % in the state of green log.
- Conversion technology from solid solution to solid.
- Moisture removal by heat under reductive atmosphere, and fixation of wood tissue by thermochemical reduction.
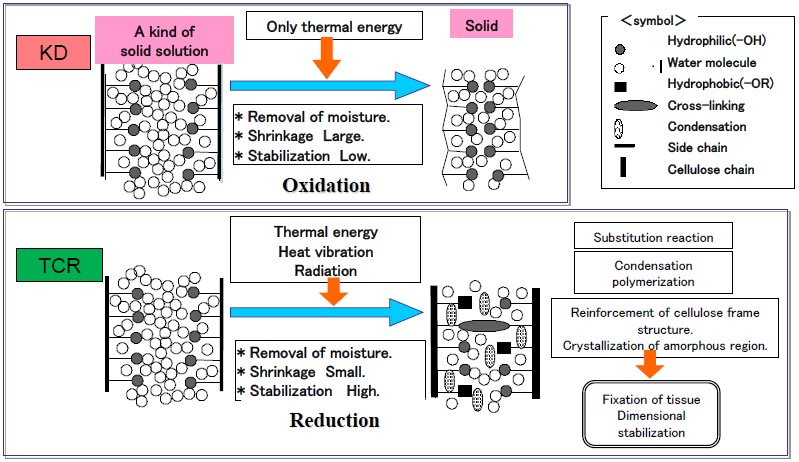
(6) Latent heat
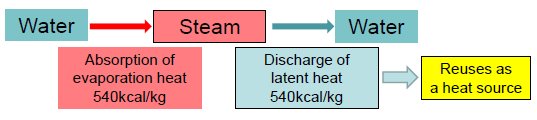
- When becoming steam, water in the lumber absorbs the evaporation heat from surroundings.
- This steam returns to water again in the lower side of furnace when this steam circulates in the furnace by convection, and at this time, the calorie acquired as evaporation heat is discharged again.
- This discharged calorie is called “latent heat”, and it is used again as a calorie.
- There is the temperature fluctuation by height in the furnace. But, the reason why the difference of the finish moisture content is small is that this latent heat can be used.
Thermal softening point to main composite of wood (°C)
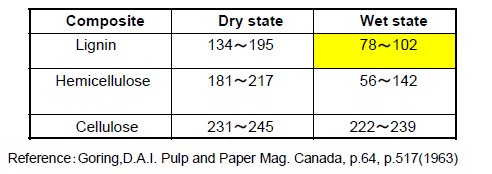
- An internal stress which is one of the deformation contributing factors of wood is the results of the strain formed in the wood cell wall.
- Cellulose fiber produces the strain, and lignin is fixed of this strain. It is clarified that thermal softening point of lignin lowers in the high moisture content of wood.
- Therefore, if the green timber of a high moisture content is efficiently heated, lignin is softened at 100 °C or less, and internal stress is relaxed by liberating strain of cell wall.
Characteristic of pyrolytic gas of wood based materials
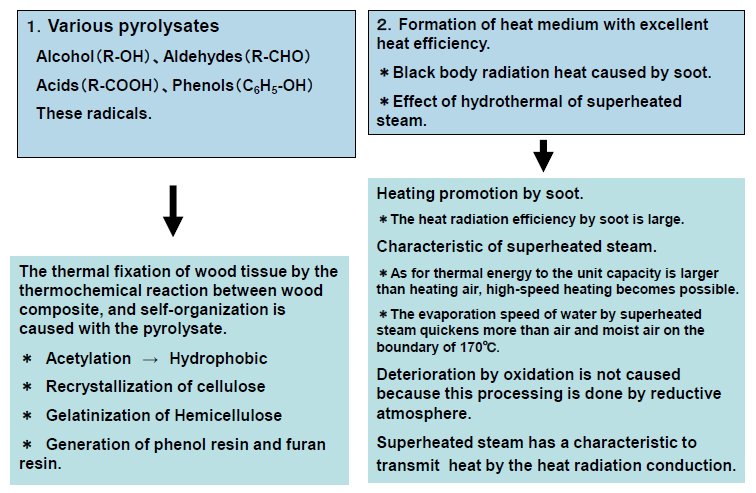
Summary of Nomura type TCR technology.
- Shape, the dimensional stabilization and dryness of wood can be done at the same time by applying the thermochemical reduction reaction with using combustion gas of wood based material under the reductive atmosphere.
- Property modification technology of wood material itself by self-organization of wood composite which is accompanied by the mutual gas —phase reaction between pyrolysis generation gas element and wood composite under reductive atmosphere.
Purpose of TCR project business
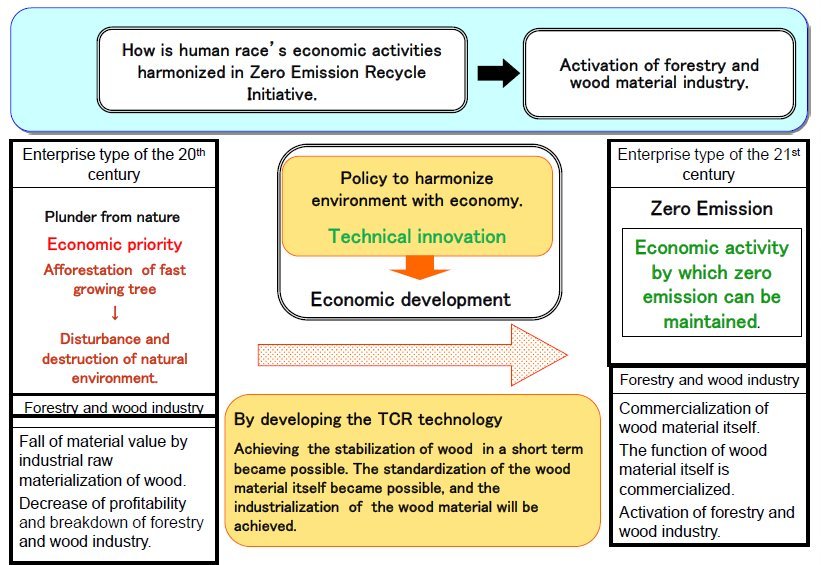
Current experience concerning Nomura type TCR technology
- 1985 The research of Nomura type TCR technology started.
- 1990 Inauguration for TCR workshop in Wood Research Institute, Kyoto University.
- 1992 No. 1 of Nomura type TCR system setting up in Fukumoku Co. Ltd. Kitakyushu City, Fukuoka Pref.
- 2000 No. 2 setting up in “Solid wood business cooperative society” in Shionoe town, Kagawa Pref.
- 2001, May Mr. Ootsuka of Malaysian emeritus consul general visited at the request of Prime Minister Mahathir. Consultation of method of using oil palm stem waste material.
- 2001, Dec. Start the research by using the experimental furnace set up in Wood Research Institute, Kyoto University.
- 2002, Mar. The experiment succeeded in the organization fixation and dimensional stabilization of oil palm lumber in only tree months for the first time all over the world.
- 2003, Nov. Oil palm zero emission project started in Malaysia.
- 2004, Sep. A basic experiment concerning the dimensional stabilization of oil palm stem waste material succeeded.
- 2006, May. No. 3 setting up in “Dreamy” Co. Ltd., Kagoshima Pref.
- 2011, Mar. No. 4 setting up in “DAC” Co. Ltd, Kyoto Pref.
Copyright © Nomura Takaya Institute, Co., Ltd. All rights reserved.